In this review, I want to introduce you to the ViV Lab Rigid Float/HA Tonearm. ViV Lab is located in Kamakura, Japan. This tonearm is the brainchild of designer Koichiro Akimoto who wanted to challenge the tonearm design world with some radical new thinking. Note, this is a two-part review, so don’t forget to take a look at Part 2 here.
Behind the Tonearm Design
So, what’s so radical? Their US distributor, Michael Fajen of Sierra Sound, nicely summarized on his website the three main design principles that make the ViV Lab Rigid Float/HA tonearm special:
“First, the tonearm is free-standing. It does not physically attach to your turntable, which means it is not directly coupled to any source of vibration or noise. It’s weighted, non-slip base is designed to provide perfect mechanical isolation. This characteristic also means the arm is compatible with a wide range of turntables as a primary or secondary tonearm, with no drilling necessary.
Second, the tonearm uses proprietary magnetized oil in the bearing mechanism. Arguably the most critical goal of tonearm design is the elimination of friction in the bearing. The material used in the Rigid Float sometimes referred to as ferro-fluid, is nearly friction-free when placed in a magnetic field. The oil also acts as a damper against acoustic vibration, further enhancing clarity and transient response.
Finally, and perhaps most importantly, the tonearm uses zero-offset geometry, making resonance optimization the top priority. The trade-off is higher tracking error at the beginning of the disc, but the advantage is the elimination of bias force, making anti-skate unnecessary. Groove modulation is never constant across the face of a record, yet conventional tonearms force the user to choose a fixed anti-skate force, placing the cartridge into a state of constant entropy during playback. The ViV Labs Rigid Float completely resolves this issue, allowing your cartridge to track with perfect lateral stability. Subtle details and textures that would otherwise be lost to resonance are reproduced clearly and beautifully.”
You can get the tonearm with either an aluminum or a carbon fiber arm pipe. It is available in three different lengths, 7”, 9” or 13”. It comes with a black metallic or gold base option. Other than the material difference of the arm pipe, the arms are identical. The ViV Lab tonearm can sit on the plinth of the turntable. It can also set off to the side on a supporting base.
NO OFFSET… UNDERHUNG…. WHAT???
Before I go any further, this review is going to require some work on your part. I am going to ask you to set aside your preconceptions and your biases. This is harder to do than you may think. I find, as a reviewer, it is one of the most difficult things I have to do when I am reviewing products. On the other hand, I find it very rewarding to be open to new ideas.
Now I admit that I am not an expert in tonearm geometry but after 45 years of playing around with this stuff, I have a pretty good grip on tonearm set up and sound. I will give you a quick summary that should carry you through the review. If you want to delve deeper into the math, I am not your guy.
Virtually every pivot tonearm is designed to try to compensate for the reduction of tracking error and the resultant skating force that is produced. Skating force is the force that constantly wants to “pull” the arm toward the center of the album when the arm is not tangent to the groove and is aggravated by the overhang geometry that is introduced to correct for the headshell offset. This force potentially increases as the cartridge progresses through the tracking arc on the album.
Addressing Tracking Error and Skating Force
Most arms designers address tracking error and skating force in two ways:
- They design the tonearm geometry with an offset headshell or an s-shaped arm pipe and use tracking geometry that incorporates “stylus overhang.” When done correctly, you get two points on the tracking arc where the stylus is tangent with the groove, and the tracking error is zero.
When you set up an arm using the tracking geometries we are all familiar with, Baerwald, Lofgren, Stevenson, or any other, all you are doing is changing where the two zero-tracking angle points fall on the album. On all other points on the album, you have tracking error up to 2 degrees or more. Unfortunately, the design introduces skating force, a new problem that has to be addressed. That brings us to point number 2. - To compensate for the skating force, designers have used numerous ways to apply an offsetting force (anti-skating) to cancel the skating force introduced by the overhang geometry. Several solutions have been used, such as magnetic anti-skating, weights with strings, springs, etc.
With the Rigid Float tonearm, designer Koichiro Akimoto decided to ignore the tracking angle distortion issue. He focused on reducing/removing the skating bias forces that he maintains are more detrimental to the sound quality than the tracking error.
About Skating Force
Conventional thinking would tell us that an arm with a higher tracking error like the ViV Lab tonearm has to be going down the wrong road, right? Well, not so fast. As it turns out this skating force that designers are trying to correct for is not a fixed value nor is it in line with the pivot point of the tonearm. It is a DYNAMIC value that varies with literally every modulation of the groove.
Until now, I have only seen two designs that can account for a changing dynamic skating force in real-time. The first is a correctly implemented straight-line tracking arm. The second is the Thales or new KL Audio tonearms that constantly adjust the headshell angle to maintain tangency as the arm moves thru the tracking arc. This is because these tonearms have no skating force to deal with. All other tonearms apply a fixed value that changes slightly throughout the arc of the album but not within each groove nor in real-time.
So, in trying to correct for the skating force that is introduced, what you end up with is a constant force value (applied anti-skating) trying to correct for a dynamic force value. This is a compromise that applies several conflicting torsional forces to a VERY sensitive device (your cartridge). Tonearm designer Akimoto-san firmly believes, “The offset angle and overhang seriously affect sound quality because of fluctuations in skating side force that can never be canceled by anti-skating mechanisms.”
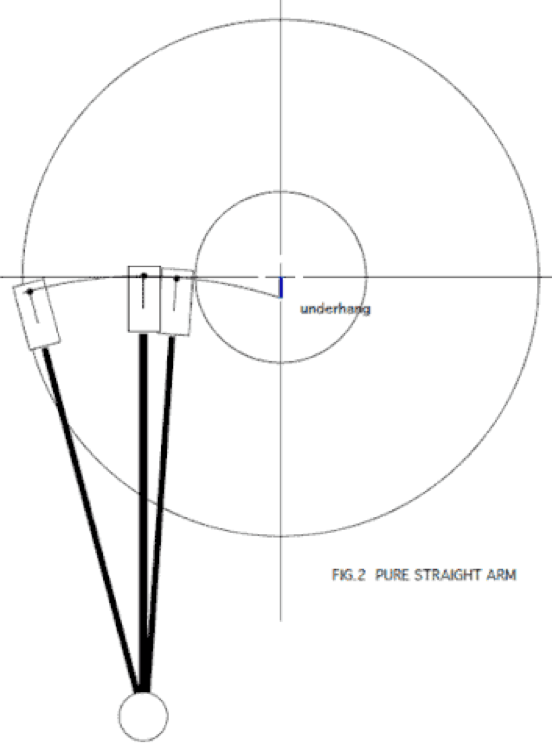
Underhung Geometry
The underhung geometry of the ViV Lab tonearm design greatly reduces skating forces but it increases the tracking error. As always, there is no free lunch. However, I can tell you from my listening that the tradeoff is well worth it sonically.
Mike Fajen explains, “I think it is worth noting, with the ViV Lab design, the point on the record at which you see the highest tracking error is the very beginning of the record. You can see this in the attached illustration of a single null point alignment. This is advantageous because this section of the record has a much higher circumference, therefore, the information cut into the groove is spread out over a much larger space per rotation.
So, the inherent potential for distortion is at its absolute lowest during this section of the record. When you track in about an inch and the circumference starts to get smaller and the grooves more tightly packed with information, by then your tracking error is on par with more conventional designs. So, the ViV lab arm very strategically places its highest point of tracking error at the part of the record where it can do the least harm.”
“Straight Line” Sound
Those of you that follow my writing know that I have a personal preference for tangential tracking tonearms. But until I auditioned the ViV Lab Rigid Float tonearm, I thought the characteristics that drew me to the “straight line sound” were the result of the lack of tracking error that a straight arm has the potential to do. And in a way it is, but it is not the lack of tracking error itself. I now realize that reducing skating bias forces on the cartridge results in the sound I like.
So what is this straight line sound? First and foremost it a feeling of effortlessness. It’s as if the cartridge is free to operate in the groove and not fighting something all of the time. Next, there is consistency in the overall presentation from the first groove to the last. It is a very dynamic sound with rock-solid stability both in tonal quality and in the soundstage it presents.
On another note, after 5 years of development and research, Yamaha, a company with a sizable R&D department and impressive musical chops decided to go down the same road. They use zero-offset underhung tracking geometry in their latest tonearm design for their Reference GT5000 turntable. That alone was enough to activate my curious nature and made me want to investigate this further. I’m glad I did.
What is a Rigid Float Bearing?
The overall design of the bearing is ingenious in my opinion. It is my understanding that what you fundamentally have is a “ball joint”. Very much like a ball sitting in a bowl-shaped cup. Not like the “golf ball in a cup of silicone” design of the Well Tempered Turntable. This is quite different. No silicone here and no ball dangling from a wire.
The ball sits/floats or more accurately stated, magnetically levitates, in a complementary-shaped cup in a bath of Ferrofluid. This fluid does two things. It decouples the ball from touching the cup, yet it provides a magnetic separation of the ball from the cup. In one design Akimoto-san has decoupled the arm from vibrations traveling up the arm from the turntable base. He also decoupled the arm from vibrations generated by the stylus. These vibrations are normally reflected back into the arm by the mechanical bearings found on most arms.
The design also keeps the arm from having the dreaded “unipivot twist or rocking”. He describes it this way. “As oil is magnetic liquid, the single fulcrum point is positioned as horizontal center spin stem floats in bearing suspension cup, composed by a doughnut-like bowl-shaped magnet, just like a round-shaped ball is fixed in the center of a cup”
Akimoto-san keeps a number of the details of the bearing design close to the vest. I didn’t learn about the bearing ferrofluid viscosity and a few other details, for example. However, here is a link that shows the basic construction of the bearing.
The ferrofluid used in the bearing can be shipped in the open bearing housing with the tonearm. The magnetic properties of the fluid do not allow it to “spill out.”
I’ll Second That
A number of you that I have corresponded with have asked me about the idea of adding a second tonearm to your turntable, many times with it in mind of using a mono cartridge. Most of the time that would involve changing out your turntable to get the ability to add a second tonearm which is a MAJOR expense both in dollars and in system setup and configuration.
With the Viv Labs design, you can easily add a second arm to your current turntable without having to swallow the “financial pill” of changing out the entire turntable. However, I will warn you, once you hear the ViV labs arm it may quickly become your primary arm.
Conclusion
Well, this is probably more than enough of the technical details. Watch for Part 2 of this review in a few days where I will go into how this tonearm sounds!
Tonearm pricing as follows:
I am told there will most likely be a 10% price increase in January 2021
Aluminum:
HA-7 $3200 retail
HA-9 $3500 retail
HA-13 $4000 retail
Carbon:
CB-7 $5500 retail
CB-9 $6000 retail
CB-13 $6500 retail